宿遷優(yōu)質(zhì)全自動鉆孔機哪家好
發(fā)布時間:2023-12-06 00:35:55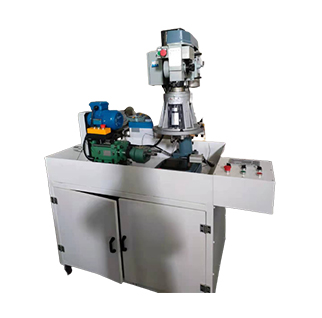
宿遷優(yōu)質(zhì)全自動鉆孔機哪家好
自動攻絲機是根據(jù)加工中心原理設(shè)計的,實現(xiàn)了加工過程中的高速、高效、高精度。與上一代數(shù)控攻牙機相比,加工效率提高了2-3倍,并具有單次和連續(xù)動作、等待時間設(shè)定、快速推進等多種模式。高精度滾珠絲杠,無間隙,雙伺服電機運動精度高;智能控制,操作簡單,重復(fù)精度0.02mm。使用攻牙油減少摩擦。在攻絲、鉆孔等金屬切削過程中使用自動攻絲機時,不能避免摩擦產(chǎn)生的廢屑。除了使用潤滑性強、摩擦系數(shù)低的攻牙油減少弓箭與攻牙、道具之間的摩擦外,還對攻牙油進行過濾和循環(huán)。

宿遷優(yōu)質(zhì)全自動鉆孔機哪家好
攻牙機屬于一種硬件機械設(shè)備,常用于產(chǎn)品的一些攻牙加工工作。如果機器運行不正常,那么即將展示完美的產(chǎn)品很可能會造成損壞并浪費半成品。分為半自動和全自動。這兩種攻牙機結(jié)合起來并向您介紹一些操作過程。您可以詳細查看它,以避免因操作不當和機器操作而造成的損壞。Di一點是在啟動之前的一些準備工作。首先,檢查攻牙機各部分是否齊全,潤滑油是否充足,機器上的螺釘是否松動,鉆頭是否損壞或鉆頭是否鋒利。其次,正常啟動時的一些預(yù)防措施。當機器開機時,在正常運行的1-2分鐘內(nèi),看機器是否會有一些噪音或某些異?,F(xiàn)象,然后慢速慢增加速度。
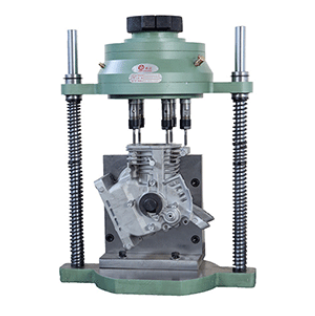
宿遷優(yōu)質(zhì)全自動鉆孔機哪家好
1、自動攻絲機床表面及盲區(qū),拆卸各堵蓋,規(guī)定內(nèi)外清理、無生銹、無黃袍,漆見原色鐵見光。清洗滑軌面及消除工作中櫥柜臺面毛邊。檢查補足螺絲、足球、手板模型,檢查各搖桿靈便穩(wěn)定性。 2、主軸軸承下刀箱維護保養(yǎng):檢查油品,保持穩(wěn)定,剩余油符合規(guī)定。消除主軸軸承錐孔毛邊。清洗液壓機調(diào)速系統(tǒng)軟件、油水分離器網(wǎng),調(diào)節(jié)汽壓。3、拐臂及升降機夾緊機構(gòu)檢查:檢查調(diào)節(jié)升降系統(tǒng)和夾緊機構(gòu)做到靈巧靠譜。

宿遷優(yōu)質(zhì)全自動鉆孔機哪家好
自動攻絲機之所以能夠在現(xiàn)代社會當中得到極大的發(fā)展,是與其自身所具有的眾多的優(yōu)勢分不開的。那么,的優(yōu)勢都包括哪些呢?一、可以說是一種高度自動化的設(shè)備,在使用和操作的時候都是非常的簡單和方便,能夠節(jié)約更多的人力物力資源,起到一個更好的使用效果。二、從整體上面而言,價格是比較便宜的,具有很大的經(jīng)濟實惠的優(yōu)點,這樣除了能夠節(jié)約更多的金錢方面的成本之外,也能夠方便人們高效率的開展自己的工作。三、在準確度方面是非常高的,能夠在保證速度快的同時也能夠保證工作的準確度。

宿遷優(yōu)質(zhì)全自動鉆孔機哪家好
高精密攻牙行程調(diào)整簡單,自動反轉(zhuǎn)裝置可自由調(diào)節(jié)攻牙行程,淺孔及有孔的低加工零件易于調(diào)整,雙重安全裝置可防止絲攻損傷(折損),主軸回轉(zhuǎn)與上下、進退刀特設(shè)雙安全離合器,主軸可自動停止,逆轉(zhuǎn)退刀不損傷刀具。齒距A,B齒輪配合A,B轉(zhuǎn)軸與主軸完全配合,依齒距推進,垂直穩(wěn)定,精密度特別高,螺絲攻牙時前后不需出力即可自如運轉(zhuǎn)。而且同時決定加工好的物品,不會產(chǎn)生粗細不同的螺紋,針對薄板和輕質(zhì)金屬,合成樹脂等軟質(zhì)物品也能攻出高級螺紋。配置多軸器可實現(xiàn)多軸同步加工,大大提高了生產(chǎn)效率。主軸進退刀是依牙距自動精密配合,工作時不浮起。

宿遷優(yōu)質(zhì)全自動鉆孔機哪家好
是一種利用多軸機床同時攻絲2-18個孔的機床。它是提高工作效率和節(jié)約生產(chǎn)成本的設(shè)備之一。在加工過程中,不可避免地會產(chǎn)生物體圖案的一些偏差。但控制加工質(zhì)量很重要。偏差越小,產(chǎn)生的圖案越精細。下面來詳細介紹自動攻絲機工作時如何提高加工質(zhì)量。在加工過程中,工藝系統(tǒng)會出現(xiàn)各種誤差,進而改變刀具與工件在切削運動中的方位關(guān)系,影響零件的加工精度。這些誤差與工藝系統(tǒng)本身的布局和切割工藝有關(guān)。產(chǎn)生誤差的主要原因有:工藝系統(tǒng)的誤差包括排樣方法的原理、機床的誤差、調(diào)整誤差、工裝夾具的制造誤差、工件的裝置誤差以及工藝系統(tǒng)磨損引起的誤差;工藝系統(tǒng)應(yīng)力變形引起的誤差;工藝系統(tǒng)熱變形引起的誤差;工件內(nèi)應(yīng)力引起的誤差。